Yesterday, I took my lunch break later in the afternoon, and I hopped onto the bus for a short trip to
Dalston - home of
Ridley Road Market (the
market is located opposite Dalston Kingsland Train Station and beside Kingsland Shopping Centre).
The market has several African fabric 'n' textiles stalls and shops, it also has 3 more mainstream style fabric retailers, and a trims shop too (see below for links). The rest of the market is a bustling and vibrant array of fruit 'n' veg stalls, kitchenware, foods of the world, toys and DVDs etc.
In total I managed to pick up 3 pieces of fabric (8 metres worth), 4 cones of overlocker (serger) thread, 2 zips, a ball of acrylic
*wool, 2 pieces of black elastic, 6 large spools of thread and a pair of second-hand jeans. Not bad for the Princely sum of £31.86 :)
Blue Fabric - from
Hamid for Fabrics £2 / metre, 2.5 metres 100% cotton.
Feels light weight, but not too thin - the colour finish puts me in mind of Chambray (which I'm always a sucker for buying!).
Red Fabric - from Stall No. 118 (I think the stall is called
Vawda's Textiles ?) in the Market, 3 metres of 100% cotton for... £1 / metre! It has a subtle sheen, and a lovely soft drape - I'm thinking nice blouse / top.
Purple and Light Blue Cones £1.50 each ,
Black Elastic 50p each and 6
Thread Spools 75p each - from
U & I Trimmings.
The 6 spools are for taking with me to sewing classes (smaller and lighter than cones dontcha know - but won't run out half-way through!) - as my preferred method for toile / muslin making on test garments is to thread trace my seam allowance lines and hems in black, and then to baste together in pale green - any subsequent changes to seam/stitching lines are made in red, then blue - before re-stitching together again in the pale green. This way I can see history and provenance of any changes I make clearly as I progress :)
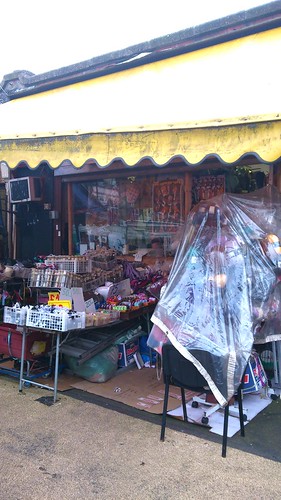
'U & I' is a funny little shop - it is very crowded with ribbons, bias bindings, rick-rack, laces, and trims inside (there's barely any room to move), and outside there's tonnes of zippers, cones, thread spools, a few colours of wool (not real wool though), buttons etc.. Things are kinda lumped together into groups, and you really have to rummage around for what you want - for example the zips are jumbled together into boxes, they're not sorted by size / colour so be prepared to dig around. But as things are so cheap you might be surprised by what you turn up!
Yellow Gingham £3 / metre, 2.5 metres plus a ball of
Acrylic Wool for £1.69 from
Dalston Mill Fabrics. It's a woven Gingham rather than a printed one. And, unlike many printed cheap Polycotton Gingham's it feels more drapey (not overly crisp and stiff) - and not at all too thin. So, I think it might be a 100% cotton too perhaps? This fabric is destined for a special project at the mid to end of August ;)
I like '
Dalston Mills Fabrics' (
links to their online shop) - it's like a
Tardis inside. The front has a big display of PVC/Vinyl Oilcloth fabric, and also a bunch of de-enveloped patterns for if I can recall correctly £1 (maybe £2?) each. The patterns are not in any organised order though, so you won't find say all the skirts together or anything handy like that. Inside there is a much bigger retail space, and a vast array of fabrics (
sorry no pics of inside - I'll ask next time if they don't mind me sneeking a few!). There's wools, and lots of buttons towards the back. But at the very back are 2 smaller-rooms. One room is full of ribbons, elastics, trims - and lady behind a counter to cut them for you (you pay at the 1 till point in the centre of the shop). The other room has their wools and suitings - it's here that I found the 100% wool fabric I used to make my
homemade pressing tools. They also have lots of zips, including long separating zippers for jackets etc. There's threads too, plus they have new Big-4 patterns inside + Burda too. The staff are always extremely friendly and helpful here too.
Then, a short walk heading South down Kingsland Road I popped into the quirky
William Gee shop and picked up 2 more overlocker
thread cones in
Pale Yellow and Pink for £1.20 each. This was my 2nd visit to their store.
'William Gee's' bricks 'n' mortar shop is a stark contrast to their snazzy
website is waaaay better than the store - I was a bit disappointed by the up close 'n' personal experience first hand. The staff
seem nice enough, but I was surprised when on my 1st visit a few weeks back that they didn't have any lingerie or FOE (fold over elastic) :( which I'd hoped to use to make
Zoe's FREE vest pattern. But fret ye not, eBay came to my rescue LOL! From their wall displays inside, and their window displays outside they carry a good range of shear, scissors, tools and rulers - including the
love it or hate it Pattern Master. (See here for their range of
Pattern Room Equipment & Design Aids.) The store was a single room - with old fashioned glass-topped counters either side (with 2
staff behind the counter) and it was devoid of all natural light. Unless it's within easier reach on a shelf (e.g. thread cones), you have to ask to be shown what you're looking for, so it's not a very consumer-focused retail experience really. I'd say don't go there to browse, go with a specific item in mind, or even better ring them up first to check they have it in stock to save you a wasted journey! (Or shop there on line hehe!)
Some other reviews of William Gee are linked at the bottom of my post. The company has been around since 1906!
And, practically next door is a big-ish sized
Oxfam shop where I grabbed 2
Royal Blue zips for 39p each (brand new stock too!), and a pair of
second-hand jeans for £2.99 - the jeans will get
refashioned methinks (
that's if I feel brave enough to get my pale 'n' pasty pins out whilst there's still a smidgen of summer left in the air!) :)!
*Nope I'm not taking up knitting or crochet LOL (there's not enough room in my little house for all the trappings of any more hobbies hehe!). It's to make the "hair" for a little dolly I'm making for my darling niece who has just turned 1 year old!
More reviews of WILLIAM GEE:
I did a quick Google search and I found these blog posts:
Set squares at the Scariest Shop in the World from 'One Foot in the Hull'.
Fabric Shopping in Dalston from 'Nicole Needles - Adventures in Sewing'.
Haberdashery from REAL shops! from 'Making My Tennant Coat'.
One gimp please from 'Sew Far Sew Good'.
This is an actually good read about the history of the place:
At William Gee Ltd, Haberdashers from 'Spitalfields Life'.
Quote from this blog:
The Lonely Crafter’s Guide to London from 'Cargo Cult Craft'.
- William Gee on the
Kingsland Road supplies haberdashery and equipment to the tailoring
trade, but their shop, unless they’ve undergone a serious revamp
recently, is one of the saddest retail spaces I’ve seen in my crafty
travels. Difficult to navigate unless you know what you want, but they
do have a pretty comprehensive range of professional tools, up to and
including tailor’s canvas and pattern design and drafting supplies. 520-522 Kingsland Road, E8.